На электропоезде ЭП2Д установлена система пассивной безопасности. Система пассивной безопасности предназначена для защиты электропоезда и пассажиров в аварийных ситуациях. Система должна срабатывать при столкновении единиц подвижного состава без предварительной подготовки электропоезда к удару и каких-либо действий со стороны локомотивной бригады.
Элементы системы обеспечивают упругое поглощение кинетической энергии в процессе движения и поглощение кинетической энергии удара в аварийных ситуациях за счет необратимой деформации крэш-элементов одноразового действия.
На электропоезде используется два вида автосцепных устройств: головная пассажирская автосцепка ТМ132 с поглощающим аппаратом Т-8П и крэш-буфером ТМ134 (рисунок 2.1.2), межвагонное беззазорное сцепное устройство БСУ-ТМ 136 для сцепки вагонов исполнений 08 и 09 (активного и пассивного типа с замками быстрого расцепления) с поглощающим аппаратом Т-7П-01 и крэш-модулем ТМ135 (рисунок 2.1.9).
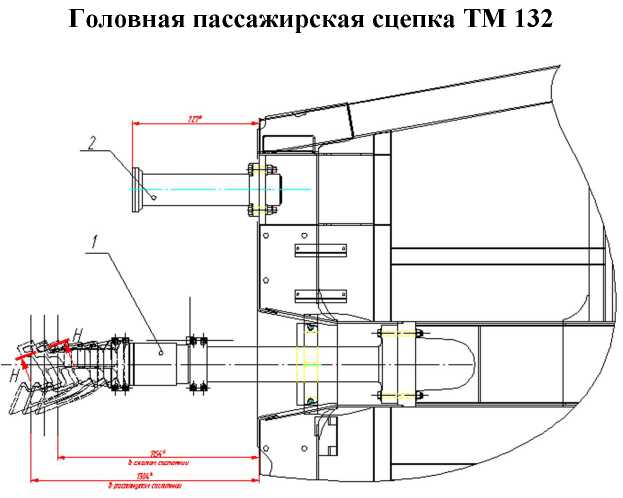
Рисунок 2.1.2 – Расположение автосцепки 132 с крэш-буфером в головной части кабины машиниста: 1 – автосцепка головная пассажирская ТМ132; 2 – крэш-буфер ТМ134
Автосцепка ТМ132
Сцепка предназначена для установки на лобовую часть головного вагона электропоезда. Сцепка обеспечивает надежное сцепление головного вагона электропоезда с вагонами, оборудованными автосцепкой СА-3 с контуром зацепления по ГОСТ 21447, и служит для передачи тяговых и тормозных усилий. Сцепка обеспечивает упругое поглощение кинетической энергии в процессе движения и поглощение кинетической энергии удара за счет необратимой деформации части сцепки (КРЭШ-элемента) при аварийном столкновении головного вагона с препятствием.
Основные технические характеристики сцепки
Наименование показателя | Значение |
Вариант исполнения | ТМ132 |
Поглощающий аппарат Т-8П эластомерный упругого типа по Т8П.00.00.000ТУ | Т8П-02 |
КРЭШ-модуль: | |
– ход, мм +5 мм | 1014 |
– усилие, МН +5% | 2000 |
– энергоемкость, МДж+10% | 2.03 |
Габаритные размеры, мм: | |
длина + 5 | 2250 |
ширина + 5 | 510 |
высота +5 | 440 |
Масса, кг +5% | 470 |
Сцепка (рисунок 2.1.3) состоит из головки автосцепки 1, поглощающего аппарата 2, КРЭШ-модуля 3. Головка сцепки 1 с поглощающим аппаратом 2 и КРЭШ-модуль 3 с поглощающим аппаратом 2 соединяются между собой клеммным соединением, состоящим из клеммы 4, стянутого 4-мя болтами с гайками.
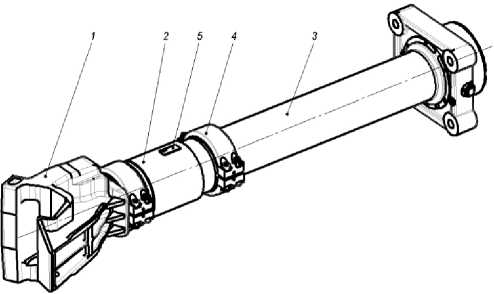
Рисунок 2.1.3 – Сцепка ТМ132: 1 – головка автосцепки; 2 – поглощающий аппарат; 3 – КРЭШ-модуль; 4 – клемма; 5 – заводская табличка.
Головка автосцепки состоит из корпуса головки 1 и приваренного к нему фланца 2 (рисунок 2.1.4). Сварное соединение усилено косынками 3.
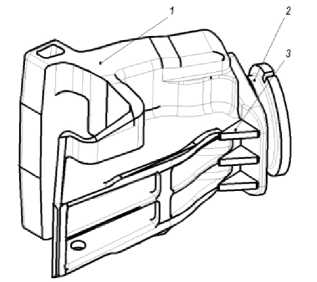
Рисунок 2.1.4- Головка автосцепки: 1 – корпус головки; 2 – фланец; 3 – косынка
Поглощающий аппарат Т-8П-02 (рисунок 2.1.5) состоит из полукорпусов 1 и 2. Шпилька 3 зафиксирована в полукорпусе 2 стопорным винтом. На шпильке 3 между полукорпусами 1 и 2 установлен эластичный пакет, состоящий из эластичных элементов 4, между которыми имеются промежуточные диски 5, а по торцам пакета – концевые диски 6. Полукорпус 1 может свободно перемещаться по шпильке 3. На шпильке 3 размещены эластичные элементы 7 и концевые диски 8. Весь пакет зажат гайкой 9, которая фиксируется болтом и, дополнительно, скобой 10.
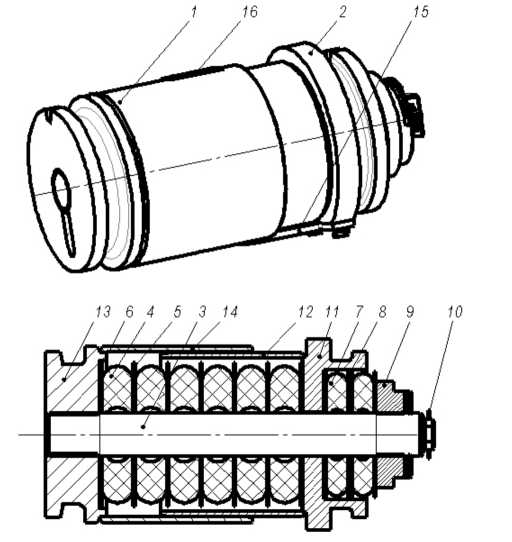
Рисунок 2.1.5 – Поглощающий аппарат Т-8П: 1 – полукорпус; 2 – полукорпус; 3 – шпилька; 4 – эластичный элемент; 5 – промежуточный диск; 6 – концевой диск; 7 – эластичный элемент; 8 – концевой диск; 9 – гайка; 10 – скоба; 11 – фланец; 12 – труба; 13 – фланец; 14 – труба; 15 -планка; 16 – табличка паспортная
Полукорпус 2 состоит из фланца 11 и приваренной к нему трубы 12, а полукорпус 1 – фланца 13 и приваренной к нему трубы 14. Также к полукорпусу 2 болтами крепится Т-образная планка 15, выполняющая роль шпонки, соориентированная относительно оси трубы пальцем, зафиксированным в планке 15. Планка 15 перемещается в пазу трубы 12. На полукорпусе 1 имеется табличка паспортная 16 поглощающего аппарата.
ВНИМАНИЕ! Поглощающий аппарат настроен на усилие начальной затяжки (25…80 кН) и величину конструкционного хода.
КАТЕГОРИЧЕСКИ ЗАПРЕЩАЕТСЯ! Производить в процессе эксплуатации частичную или полную разборку поглощающего аппарата.
Крэш-модуль
Поглощение энергии происходит за счет пластической деформации (редукции) трубы фильерой. Крэш-модуль включает в себя крэш-элемент 1, соединенный с плитой 2 посредством фильеры со сферической поверхностью. Крэш-элемент 1 со сферической фильерой образуют шарнирный узел. В плите 2 также имеется ответная сферическая поверхность. Такая конструкция обеспечивает отклонение сцепки вверх-вниз и вправо-влево. Винты 3, законтренные гайкой 4, не позволяют фильере проворачиваться вокруг горизонтальной оси сцепки. В винтах 3 имеются маслоподводящие отверстия. Крэш-элемент состоит из трубы 6 и приваренного к ней фланца 5. Защиту шарнирного узла от попадания грязи обеспечивают эластичный чехол 7 и резиновый диск, закрепленные планками 8. Для подвода смазки к шарнирному узлу на плите 2 установлены пресс-масленки. На фланце 5 выполнены пазы под штифты для взаимной ориентации крэш-элемента и поглощающего аппарата.
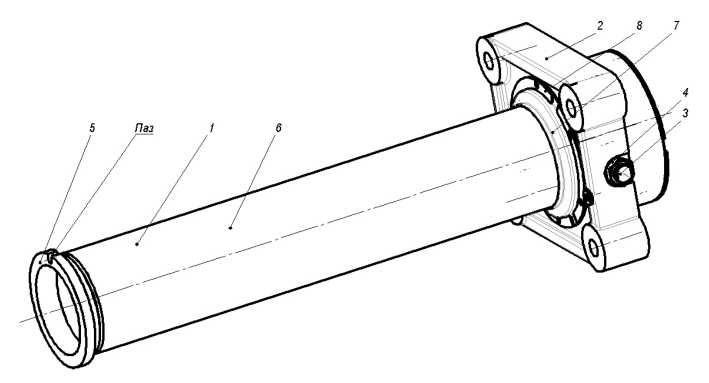
Рисунок 2.1.6 – КРЭШ-модуль сцепки ТМ132: 1 – крэш-элемент; 2 – плита; 3 – винт; 4 – гайка; 5 – фланец; 6 – труба; 7 – чехол; 8 – планка
ВНИМАНИЕ! Все крэш-элементы системы неразборные.
Запрещается в процессе эксплуатации производить частичную или полную разборку крэш-элементов. Для расцепления сцепки применяется специальный ключ.
Крэш – буфер ТМ134
Крэш-буфер ТМ134 (далее по тексту – буфер) предназначен для установки на лобовую часть головного вагона электропоезда. Буфер обеспечивает поглощение кинетической энергии за счет необратимой деформации трубы крэш-элемента при аварийном столкновении головного вагона состава с препятствием.
Буфер (рисунок 2.1.7) – это неразборная конструкция, состоящая из крэш-элемента 1 и приваренной к нему плиты 2 с зубьями для защиты вагонов от наползания друг на друга. На плите крэш-элемента закреплена табличка паспортная 3.
Буфер входит в состав КРЭШ-системы головного вагона, включающую также головную автосцепку ТМ132.
Технические характеристики буфера
Наименование показателя | ТМ134 |
Усилие деформации, кН+10% | 1000 |
Поглощаемая энергия, кДж+10% | 602 |
Рабочий ход, мм | 602+5 |
Габаритные размеры, мм: | |
длина | 853+3 |
ширина | 300-2 |
высота | 300-2 |
Полная масса, кг | 85+5% |
Буфер (рисунок 2.1.7) неразборная конструкция , состоящая из плиты противоподъемной 2, приваренной к КРЭШ-элементу 1. На КРЭШ-элементе закреплена табличка паспортная 3.
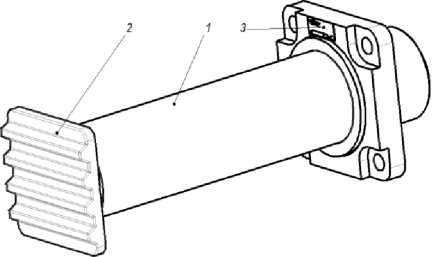
Рисунок 2.1.7 – КРЭШ-буфер ТМ134: 1 – КРЭШ-элемент; 2 – плита противоподъемная; 3 – табличка паспортная
КРЭШ- элемент (рисунок 2.1.8) состоит из трубы 1, вставленной в фильеру 2, установленную в плите 3. К плите 3 приварена направляющая труба 4. К торцу трубы 1 приварена заглушка 5. Труба 1 зафиксирована в направляющей трубе 4 прерывистым сварным швом. Вместе труба 1 и фильера 2 образуют КРЭШ-модуль. Поглощение энергии происходит за счет пластической деформации (редукции) трубы 1 фильерой 2.
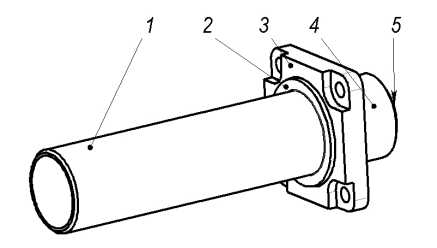
Рисунок 2.1.8 – КРЭШ-элемент ТМ134: 1 – труба; 2 – фильера; 3 – плита; 4 -направляющая труба; 5 – заглушка
ЗАПРЕЩАЕТСЯ разбирать буфер каким-либо способом в процессе его эксплуатации.
Межвагонное беззазорное сцепное устройство БСУ-ТМ136
Сцепное устройство БСУ-ТМ136 предназначено для соединения вагонов пассажирского моторвагонного подвижного состава и передачи тяговых и тормозных усилий. Для сцепления с автосцепкой СА-3 предусмотрен переходник ТМ120.01.05.007.
Как пример, установка сцепного устройства БСУ-ТМ136 показана на моторном вагоне (рисунок 2.1.9).
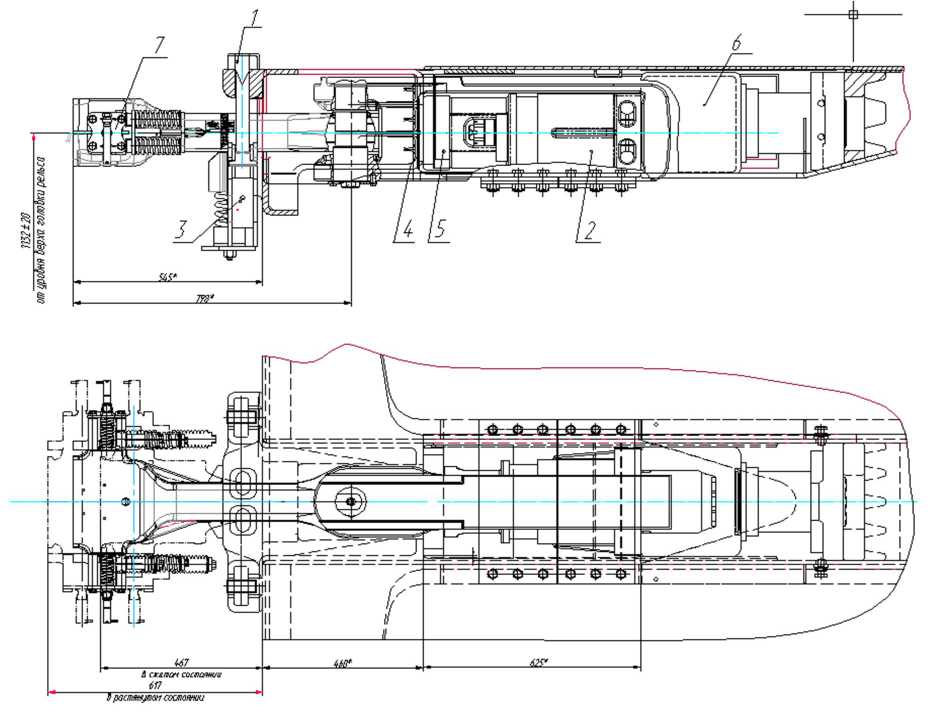
Рисунок 2.1.9 – БСУ – ТМ136 с крэш- модулем ТМ135 и поглощающим аппаратом Т-7П-01 на моторном вагоне: 1 – подвеска маятниковая; 2 – аппарат поглощающий Т-7П-01; 3 – балочка центрирующая ТМ136; 4 – узел тяговый ТМ136; 5 – плита; 6 – крэш-модуль ТМ135; 7 – корпус сцепки БСУ-ТМ136.
Технические характеристики БСУ-ТМ136
Наименование показателя | Значение |
Максимальные растягивающие усилия без деформации деталей сцепного устройства, кН | 1500 |
Максимальные сжимающие усилия без деформации деталей сцепного устройства, кН | 2500 |
Энергоемкость поглощающего аппарата при усилии полного сжатия, кДж, не менее | 5 |
Усилие полного сжатия поглощающего аппарата, кН, не менее | 1500 |
Рабочий ход поглощающего аппарата, мм | 80-5 |
Относительная скорость соударения вагонов при сцеплении, км/ч, не более | 3 |
Относительное линейное смещение осей головок при сцеплении, мм, не более | |
– в вертикальной плоскости | 70 |
– в горизонтальной плоскости | 80 |
Отклонение головок сцепок, | |
– в горизонтальной плоскости | ±15 |
– в вертикальной плоскости | ±6 |
Сцепное устройство ТМ136 включает в себя корпус сцепки 7, шарнирно с ним связанный тяговый узел 4, аппарат поглощающий Т -7П-01 (2), крэш-модуль ТМ135 (6) (рисунок 2.1.9).
На данном электропоезде используются сцепка БСУ-ТМ136-08 (исполнение 8) пассивного типа с замками быстрого расцепления типа БЗМ и БСУ -ТМ136-09 (исполнение 9) активного типа с направляющим конусом, клиновыми замками и приводом расцепным.
БСУ-ТМ136-08 (рисунок 2.1.10а) состоит из головы сцепки 1, на которой установлены замки 2 типа БЗМ, и узла тягового 3, в котором размещены плита 4 и аппарат поглощающий 5. В БСУ-ТМ136-09 (рисунок 2.1.10б) в голову сцепки 1 установлен направляющий конус 6, клиновые замки 7 и привод расцепной 8. Клиновые замки закрыты противопыльными крышками 9, которые уплотнены резиновыми прокладками 10. Голова сцепки 1 и узел тяговый 3 шарнирно соединены друг с другом. На голове сцепки 1 устанавливаются таблички паспортные 11.
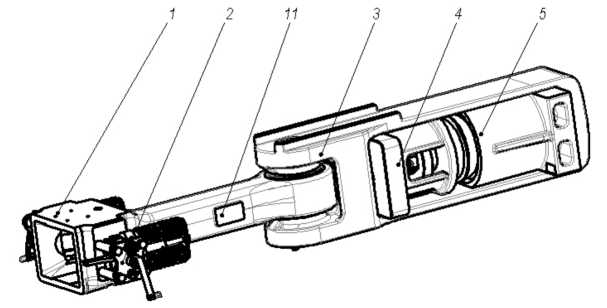
Рисунок 2.1.10а – Беззазорное сцепное устройство БСУ-ТМ136-08: 1 – голова сцепки; 2 – замок БЗМ; 3 – узел тяговый; 4 – плита; 5 – аппарат поглощающий; 11 – табличка заводская
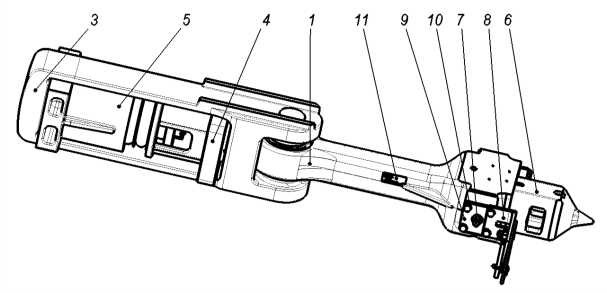
Рисунок 2.1.10б – Беззазорное сцепное устройство БСУ-ТМ136-09: 1 – голова сцепки; 2 – замок БЗМ; 3 – узел тяговый; 4 – плита; 5 – аппарат поглощающий; 6 – направляющий конус; 7 – клиновый замок; 8 – привод расцеп-ной; 9 – крышка; 10 – прокладка; 11 – табличка заводская
Голова сцепки (рисунок 2.1.11) состоит из литого корпуса 1, в котором установлен сферический подшипник скольжения 2 необслуживаемого типа. Сверху подшипник закрыт противопыльным гофрочехлом 3 с распорной втулкой 4. Конструкция допускает установку сферического подшипника обслуживаемого типа по решению Заказчика. В верхней части зева корпуса 1 установлен штифт 5, предназначенный для правильной установки переходника для маневровых работ (см. ниже). Сферический подшипник в осевом направлении зафиксирован пружинным стопорным кольцом (поз.8, рисунок 5.18).
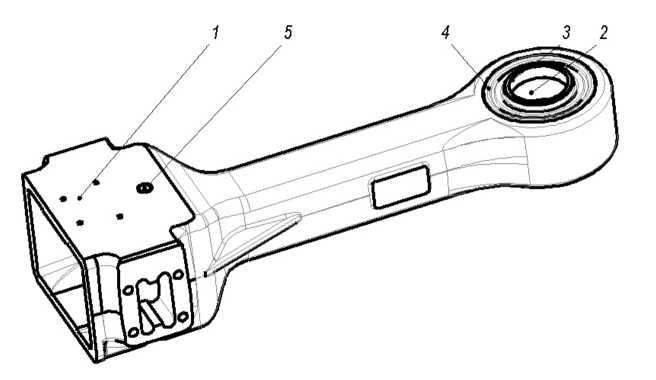
Рисунок 2.1.11 – Голова сцепки: 1 – корпус; 2 – сферический подшипник; 3 – распорная втулка; 4 – гофрочехол; 5 – штифт
Узел тяговый (рисунок 2.1.12) состоит из литого корпуса тягового 1, в котором установлен палец 2. Палец зафиксирован планкой 3. В корпус тяговый 1 ввернут упор 4, который фиксируется специальным винтом (на рисунке не показан), установленным в нижней части. Со стороны поглощающего аппарата установлен резинометаллический демпфер 5.
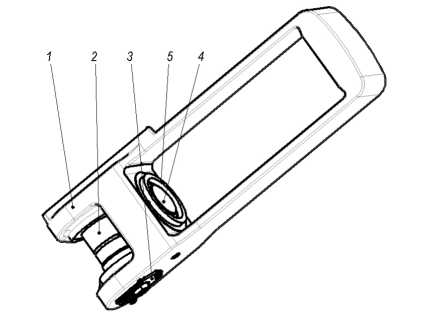
Рисунок 2.1.12 – Тяговый узел: 1 – корпус тяговый; 2 – палец; 3 – планка; 4 – упор; 5 – демпфер
Шарнирный узел соединяет голову сцепки и тяговый узел, при этом голова сцепки имеет возможность вращения по трем координатным осям относительно тягового узла на определенные углы по каждой из трех осей.
Конструкция шарнирного узла показана на рисунке 2.1.13. В узел входит палец 3, сферический подшипник скольжения 5, внешнее кольцо которого зафиксировано стопорным кольцом 8 в корпусе 1 головы сцепки, а внутреннее кольцо зажато через распорную втулку 7 между торцем посадочного отверстия корпуса тягового 2 и буртиком пальца 3. Палец 3 зафиксирован в вертикальном направлении планкой 4. Гофрочехол 6 защищает подшипник 5 от попадания грязи.
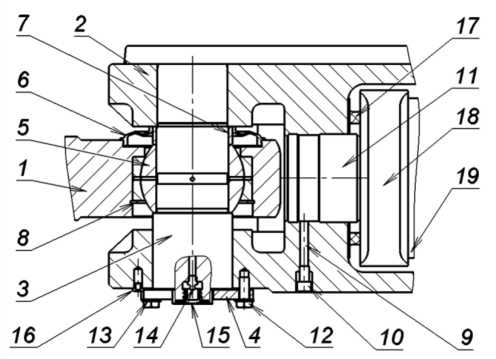
Рисунок 2.1.13 – Шарнирный узел: 1 – корпус головы сцепки; 2 – корпус тяговый; 3 – палец; 4 – планка; 5 – подшипник сферический; 6 – гофрочехол; 7 – втулка распорная; 8 – кольцо пружинное стопорное; 9 – фиксатор; 10 – винт; 11 – упор; 12 – болт; 13 – шайба; 14 -масленка; 15 – заглушка; 16 – заглушка; 17 – демпфер; 18 – плита; 19 – стакан поглощающего аппарата
Крэш-модуль ТМ135
Крэш-модуль ТМ135 предназначен для поглощения кинетической энергии при аварийном столкновении подвижного состава с препятствием и устанавливается в хребтовую балку вагона. Крэш-модуль ТМ135-01 (рисунок 2.1.14) состоит из крэш-элемента 1, кольца 4 и ползуна 2.
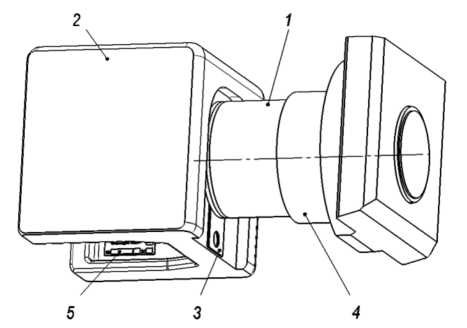
Рисунок 2.1.14 – Крэш-модуль ТМ135-01: 1 – крэш-элемент; 2 – ползун; 3 – прокладка; 4 – кольцо; 5 – табличка паспортная
Ползун соединен с крэш-элементом при помощи болтов М12. Между крэш-элементом и ползуном могут устанавливаться до трех прокладок 3, с помощью которых регулируется размер 625-3 в хребтовой балке вагона. На ползун с внутренней стороны устанавливается паспортная табличка 5. Крэш-элемент ТМ135 (рисунок 2.1.15) состоит из плиты 1 с фильерой 2. В фильеру вставлена труба 3 с приваренным к ней фланцем 4 с резьбовыми отверстиями. С другого конца труба 3 закрыта заглушкой (на рисунке не показана). Труба 3 соединена с плитой 1 прерывистым сварным швом.
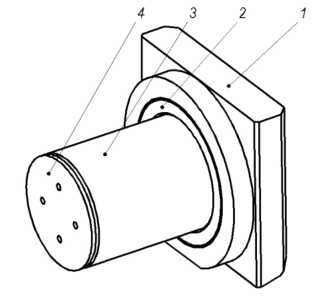
Рисунок 2.1.15 – Крэш-элемент ТМ135: 1- плита; 2 – фильера; 3 – труба; 4 – фланец
Для вагонов электропоезда ЭП2Д используется крэш-модуль ТМ135-01 с ходом крэш-элемента 130 мм. Ход крэш-элемента определяется длиной проставочного кольца 4 (рисунок 2.1.14).
Аппарат поглощающий Т-7П-01
Аппарат поглощающий Т-7П-01 (далее по тексту – аппарат) предназначен для рассеивания энергии удара при маневровых операциях, смягчения ударов и рывков и уменьшения вредных динамических воздействий на конструкцию вагона и пассажиров в процессе движения электропоезда.
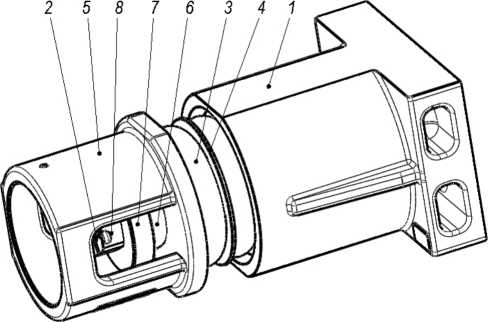
Рисунок 2.1.16 – Аппарат поглощающий Т-7П-01: 1 – основание; 2 – болт; 3 – элемент эластичный; 4 – диск; 5 – стакан нажимной; 6 – демпфер; 7 – диск нажимной; 8 – гайка.
Аппарат (рисунок 2.1.16) состоит из литого основания 1 с цилиндрическим корпусом. В корпусе размещен пакет эластичных элементов, состоящий из полимерных тел вращения – элементов эластичных 3 и дисков 4. На пакет эластичных элементов устанавливается стакан нажимной 5, эластичный демпфер 6 и диск нажимной 7. Все перечисленные детали стягиваются стяжным болтом 2 и корончатой гайкой 8, законтренной шплинтом.
Особенности конструкции деталей и узлов элементов системы
Конус центрирующий (рисунок 2.1.17) представляет собой литую деталь с четырьмя окнами для стопоров замков и двумя пазами для правильной ориентации при сборке
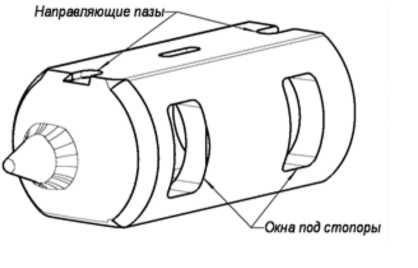
Рисунок 2.1.17 – Конус центрирующий
Клиновой замок (рисунок 2.1.18) состоит из замка, как узла, и стопора 3 с резьбовым отверстием. Замок состоит из штока 1 с резьбовым концом, стопора 2 с гладким отверстием, регулировочной 4 и контровочной 5 гаек.
На стопорах 2 и 3 имеются отверстия А для ориентации замка при установке его в корпус головы сцепки. При правильной установке замка отверстия А должны быть обращены в сторону плоскости сцепления.
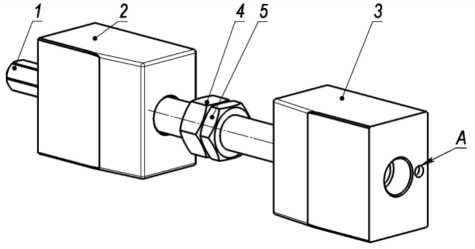
Рисунок 2.1.18 – Клиновой замок: 1- шток; 2 – стопор с гладким отверстием; 3 – стопор с резьбовым отверстием; 4 – гайка регулировочная; 5 – гайка контровочная.
Замок быстрого расцепления типа БЗМ
Хвостовик 13 стопора 1 вставлен в центральное отверстие пластины 3 и на его конце закреплен резьбовой наконечник 2. Между фланцем 4, который является частью хвостовика 13 стопора 1, и пластиной 3 на трубках 15 установлены две пружины 5. Направляющие трубки 15 расточенным концом вставлены в отверстия пластины 3 и зафиксированы осями 7. На оси 7 при помощи поводка 16 свободно вращается флажок 8. Различие между правым и левым замками заключается в том, на какую из двух осей 7 установлен флажок 8. Клин 9 вставлен паз на хвостовике 13. Клин 9 имеет жестко связанный с ним хвостовик с уступом, в который упирается передняя опора 19. Хвостовик клина имеет внутреннюю резьбу под технологический болт 10. Между передней 19 и задней 20 опорами на направляющих трубках 18 установлены пружины 11, являющиеся аккумуляторами энергии. Направляющие трубки 18 пристыкованы к втулкам 17, размещенным на двух распорных втулках 14.
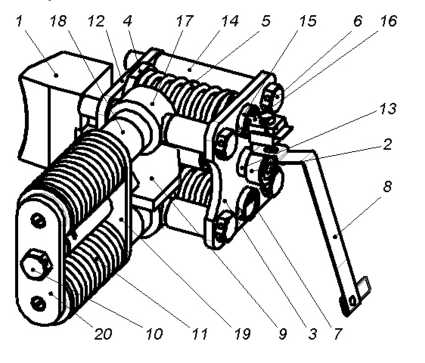
Рисунок 2.1.19 – Замок быстрого расцепления типа БЗМ: 1 – стопор; 2 – резьбовой наконечник; 3 – пластина; 4 – фланец; 5 – пружина стопора; 6 – установочные болты; 7 – ось; 8 – флажок; 9 – клин; 10 – технологический болт; 11 – пружина клина; 12 – транспортировочная пластина; 13 – хвостовик; 14 – распорная втулка; 15 – трубка; 16 – поводок; 17 – втулка; 18 -направляющая трубка; 19 – опора передняя; 20 – опора задняя
Привод расцепной (рисунок 2.1.20) состоит из двух кронштейнов 1, на которых шарнирно на осях 4 установлены рычаги 2. Рычаги 2 через оси 5 соединены тягой 3. От отклонения от нейтрального положения рычаги 2 удерживаются возвратными пластинчатыми пружинами 6, которые заправлены в петли осей 5.
При сцеплении вагонов носик клина 9 (рисунок 2.1.19) упирается в верхнюю часть рычага 2 привода расцепного (рисунок 2.1.20). При дальнейшем сближении вагонов клин 9 сжимает пружины 11 (рисунок 2.1.19). Стопор 1 при этом, скользя по клину, входит в окна конуса центрирующего и фиксирует его в голове сцепки. Сцепление произошло.
Для расцепления необходимо потянуть за нижний конец рычага 2 привода расцепного (рисунок 2.1.20). При этом перед носиком клина откроется паз, в который клин 9 будет вытолкнут пружинами 11. Перемещаясь, клин выдернет стопора 1 из окон конуса центрирующего. Расцепление произошло.
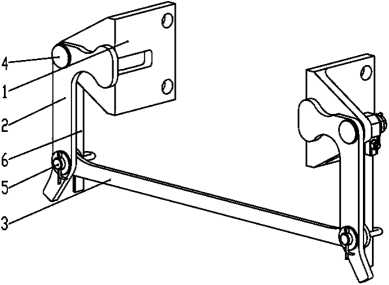
Рисунок 2.1.20 – Привод расцепной: 1 – кронштейн; 2 – рычаг; 3 – тяга; 4 – ось; 5 – ось; 6 – возвратная пластинчатая пружина
Балочка центрирующая устанавливается на передний упор хребтовой балки вагона посредством подвесок маятниковых (106.00.012-0) при монтаже сцепки.
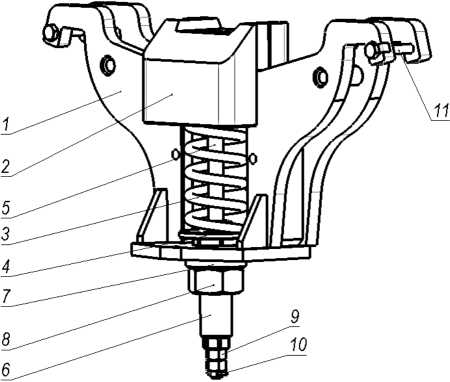
Рисунок 2.1.21 – Балочка центрирующая: 1 – корпус; 2 – опора; 3 – пружина; 4 – подпятник; 5 – шток; 6 – винт; 7 – втулка; 8 – гайка; 9 – гайка; 10 – шплинт; 11 – болт
Балочка центрирующая (рисунок 2.1.21) представляет собой корпус 1 с пружинным поддерживающим механизмом. По ребрам передних кронштейнов корпуса 1 скользит опора 2. В отверстие опоры 2 вставлен шток 5, на резьбовой конец которого навинчены две гайки 9. На конце штока 5 установлен шплинт 10. Между опорой 2 и подпятником 4 расположена пружина 3. Вращением винта 6 по резьбе во втулке 7 осуществляется поднятие опоры 2, а, следовательно, достигается необходимая высота головы сцепки над уровнем головки рельса. Положение винта 6 фиксируется контргайкой 8. Верхнюю гайку 9 завернуть до упора в торец винта 6. Заданное положение зафиксировать нижней гайкой 9.
Расцепление сцепок БСУ-ТМ136 осуществляется ключом расцепным (рисунок 2.1.22).
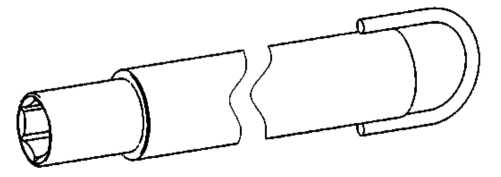
Рисунок 2.1.22 – Ключ расцепной ТТПТ06.00.000
Комплект переходников (рисунок 2.1.23) состоит из зуба 1, шкворня 2, адаптера внешнего 3, адаптера внутреннего 4 и клинового замка 5.
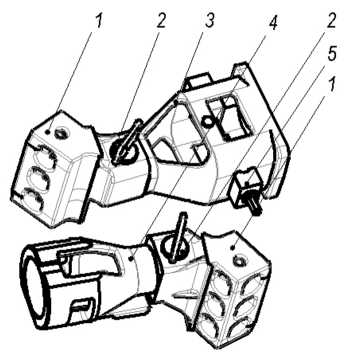
Рисунок 2.1.23 – Комплект переходников: 1 – зуб; 2 – шкворень; 3 – адаптер внешний; 4 – адаптер внутренний; 5 – клиновой замок
Работа элементов системы
Работа головной пассажирской сцепки ТМ132
Процесс сцепления и расцепления головного вагона с локомотивом или другим вагоном, оборудованным сцепкой типа СА-3, происходит аналогично сцеплению и расцеплению автосцепки СА-3. Для расцепления сцепки ТМ132 применяется ключ расцепной ТМ132.47.01.000. При сцеплении с локомотивом или другим вагоном поглощающий аппарат упруго демпфирует возможные удары в процессе сцепления. Максимальная скорость сближения сцепляемых вагонов – не более 2 км/час.
В момент столкновения состава с препятствием сначала происходит упругая деформация эластичных элементов поглощающего аппарата до полного закрытия поглощающего аппарата (75…80 мм), после этого при достижении определенной силы взаимодействия сцепки с препятствием (около 2000 кН), начинается деформация крэш-элемента сцепки с поглощением кинетической энергии столкновения.
После срабатывания крэш-элемента сцепка демонтируется с вагона и отправляется на восстановление на завод-изготовитель.
Работа крэш-буфера ТМ134
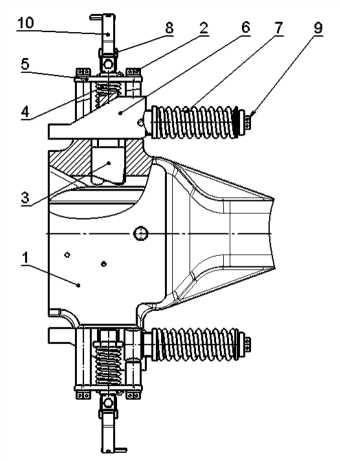
Рисунок 2.1.24 – Голова сцепки с замками типа БЗМ (исполнение 08): 1 – корпус сцепки; 2 – болты; 3 – стопор; 4 – пружина задвижки; 5 – крышка замка; 6 – клин; 7 – пружина клина (аккумулятор энергии); 8 – наконечник; 9 -технологический болт; 10 – флажок визуального контроля положения замков
В определенный момент столкновения головного вагона с препятствием начинается деформация крэш-буфера. Деформация происходит при усилии около 1000 кН на каждом буфере. После срабатывания крэш-элемента буфер демонтируется с вагона и отправляется на восстановление изготовителю. На вагон монтируется новый буфер в соответствии с настоящим Руководством.
Каждый крэш-буфер рассчитан на поперечное усилие 30 тс. Ребристая лобовая плита при столкновении препятствует наползанию одного вагона на другой
ЗАПРЕЩАЕТСЯ! Использовать буфер для буксировки вагона.
Работа межвагонного крэш-модуля ТМ135
При столкновении состава с препятствием и срабатывании крэш- элементов головной сцепки, крэш-буферов и достижения силы взаимодействия между вагонами около 2400 кН начинается поступательное движение ползунов в каждом вагоне с деформацией крэш-элемента модуля, в результате чего происходит поглощение энергии столкновения. После срабатывания крэш-модуль демонтируется с вагона и отправляется на восстановление. На восстанавливаемый вагон монтируется новый крэш-модуль.
Работа беззазорного сцепного устройства
На рисунке 2.1.24 показана голова сцепки с замками типа БЗМ (исполнение 08).
На корпусе сцепки 1 с помощью болтов 2 закреплены замки БЗМ по одному с каждой стороны (правый и левый). Клин 6 находится в прорези хвостовика замка и поджат к нему пружинами 7, являющимися аккумулятором энергии (стопора замков показаны в положении готовности к сцеплению).
Для вывода стопора 3 из зацепления, в случае его заклинивания, служит наконечник 8, установленный на оконечности хвостовика задвижки. Для этого нужно навернуть резьбовую оправку М30 (рисунок 2.1.25) на наконечник 8 и вывести задвижку замка из окна конуса.
Принудительное сжатие пружин клина 7 (например, при установке переходника) производится технологическими болтами 9.
Для визуального контроля полноты срабатывания замков предназначены флажки 8 и 11 и щитки 9 (рисунок 2.1.26).
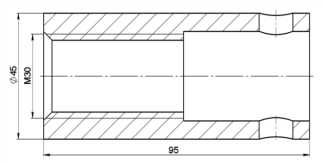
Рисунок 2.1.25 – Резьбовая оправка М30
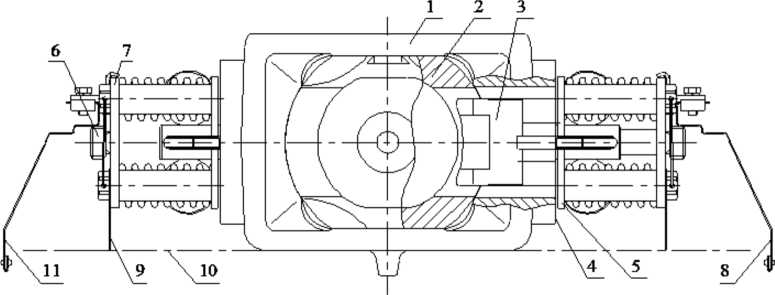
Рисунок 2.1.26 – Схема контроля полноты срабатывания замков БЗМ в сцепленном состоянии БСУ: 1 – корпус сцепки; 2 – центрирующий конус; 3 – стопор; 4 – торец окна для замка; 5 – подвижные упоры пружин замка; 6 – наконечник хвостовика штока задвижки; 7 – крышка замка; 8 – флажок; 9 – щиток; 10 – контрольная плоскость; 11 – флажок
Сцепка БСУ-ТМ136, исполнение 09, (с центрирующим конусом и приводом расцепным) показана на рисунке 2.1.106. Положение привода расцепного перед сцеплением и при расцеплении вагонов показано на рисунке 2.1.27.
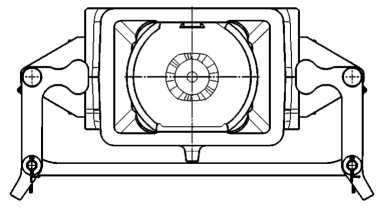
Рисунок 2.1.27 – Работа привода расцепного БЗМ-02-000 – а) положение привода расцепного БЗМ-02-000 перед сцеплением вагонов
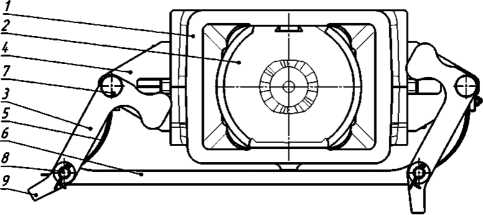
Рисунок 2.1.27 – Работа привода расцепного БЗМ-02-000 – 6) положение привода расцепного БЗМ-02-000 при расцеплении вагонов:1 – голова сцепки; 2 – центрирующий конус; 3 – рычаг; 4 – кронштейн; 5 – набор упругих пластин; 6 – тяга; 7 – ось рычага; 8 – ось тяги; 9 – концевая часть рычага для ключа расцепного
Процесс сцепления сцепок БСУ показан на рисунке 2.1.28.
Перед сцеплением необходимо убедиться, что на одном из сцепляемых вагонов установлена сцепка исполнения 08 (с замками БЗМ), а на другом – сцепка исполнения 09 (с центрирующим конусом и приводом расцепным). Рекомендуемая разность уровней осей сцепок на смежных вагонах над головкой рельса должна быть ±20 мм.
При сдвигании вагонов рычаги 3 привода расцепного надавливают на клинья замков 4, которые сжимают пружины 7, и освобождают стопоры 5. Под действием пружин 6 стопоры 5 входят в окна центрирующего конуса, обеспечивая беззазорное соединение головок сцепок.
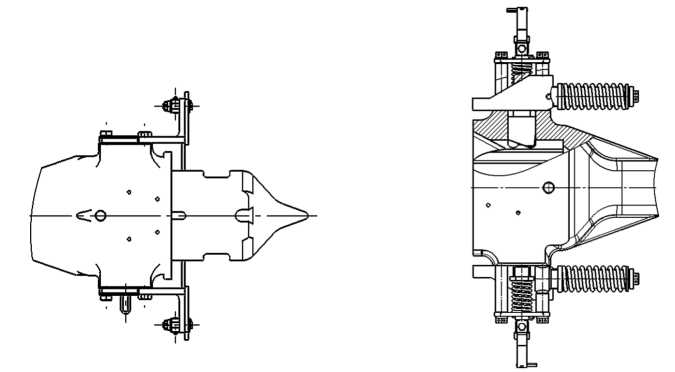
Рисунок 2.1.28 – Процесс сцепления сцепок а) исходное положение сцепного устройства перед сцеплением
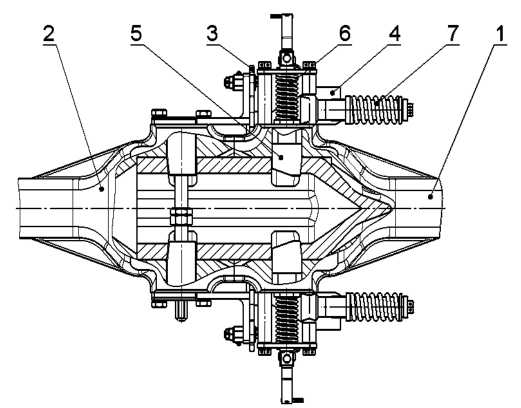
Рисунок 2.1.28 – Процесс сцепления сцепок б) сцепное устройство в сцепленном состоянии: 1 – голова сцепки с замками БЗМ; 2 – голова сцепки с центрирующим конусом; 3 – рычаг привода расцепного; 4 – клин; 5 – стопор; 6 – пружины стопоров; 7 – пружина клина
При сцеплении вагонов за счет кинетической энергии движения вагонов друг относительно друга пружинный аккумулятор энергии заряжается. При расцеплении эта энергия будет использована для передвижения клина вперед и выдвигания стопоров из окон центрирующего конуса.
После завершения сцепления необходимо без захода в пространство между вагонами:
- проконтролировать полноту срабатывания механизмов сцепления визуально, по положению флажков 8 и 11 (рисунок 2.1.26) относительно контрольной плоскости 10, проходящей по нижним кромкам щитков 9. Флажки, окрашенные в красный цвет, должны полностью располагаться ниже контрольной плоскости. При неправильном положении флажков на сцепленных вагонах допускается настройка положения флажков путем их подгибки;
- проверить отсутствие сквозного зазора по плоскости сцепления головок сцепок (рисунок 2.1.28б). Щуп толщиной 0,3 мм не должен проходить между головами сцепок хотя бы в одной точке.
При невыходе флажков полностью или частично за контрольную плоскость, вагоны расцепить и процесс сцепления повторить.
Расцепление сцепок производится без захода в пространство между вагонами в следующей последовательности:
- ключом расцепным зацепить концевую часть рычага 9 (рисунок 2.1.27) привода расцепного и, потянув ключ вверх или нажав вниз, повернуть рычаг до щелчка, свидетельствующего о срабатывании пружинных аккумуляторов энергии и выходе задвижек из окон конуса. При этом между торцами головок сцепок должен появиться небольшой зазор;
- проконтролировать факт расцепления сцепки. Визуальным признаком полного выхода задвижек из окон конуса является положение флажков 8 (рисунок 2.1.29) относительно контрольной плоскости 10. Флажки не должны выступать за нижний край щитков 9;
- развести вагоны.
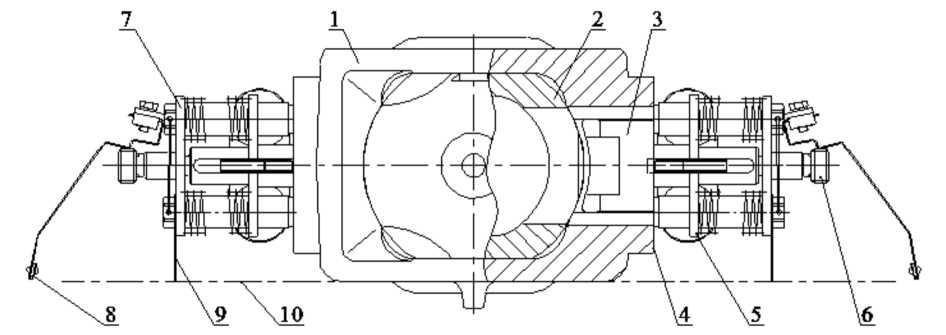
Рисунок 2.1.29 – Схема контроля полноты срабатывания замков БЗМ при расцеплении вагонов: 1 – корпус сцепки; 2 – центрирующий конус; 3 – стопор; 4 – плоскость крепления замка; 5 – подвижные упоры пружин замка; 6 – наконечник хвостовика замка; 7 – пластина замка; 8 – флажок; 9 – щиток; 10 – контрольная плоскость
В случае несрабатывания замка БЗМ нужно навернуть резьбовую оправку М30 (рисунок 2.1.25) на наконечник 8 (рисунок 2.1.24) хвостовика замка, вывести задвижку замка из окна конуса и расцепить вагоны. Выкрутить оправку и повторить сцепление. Вместо резьбовой оправки М30 можно использовать обычную стандартную высокую гайку.
Установка адаптера внутреннего в голову сцепки с замками БЗМ
Установка адаптера внутреннего в голову сцепки с замками БЗМ (рисунок2.1.30) производится в следующей последовательности:
- вращая технологический болт 6 замка 2 с помощью ключа, вывести стопоры 3 (рисунок 2.1.26) из внутренней полости корпуса 1 головы сцепки;
- установить внутренний адаптер 3 во внутреннюю полость корпуса сцепки 1 до упора;
- вращая технологические болты 6 в другую сторону, ввести до упора стопоры в пазы адаптера 3;
- полноту срабатывания замков проверить по схеме контроля (рисунок 7.3);
- установить зуб 4 на адаптер 3 и зафиксировать его с помощью шкворня 5;
- повернуть шайбу на торце шкворня на угол 30.. .70° в любую сторону для предотвращения его выпадания.
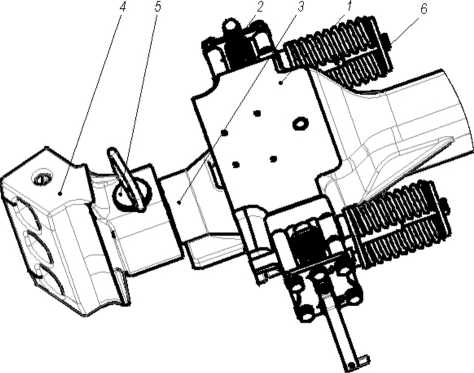
Рисунок 2.1.30 – Установка адаптера внутреннего: 1 – корпус головы сцепки; 2 – замок; 3 – адаптер внутренний; 4 – зуб; 5 – шкворень; 6 – болт технологический
Установка адаптера наружного
Установка наружного адаптера на центрирующий конус производится в следующей последовательности:
- установить наружный адаптер 3 на центрирующий конус 2;
- установить в пазы адаптера 3 и центрирующего конуса 2 клиновой за-мок 6, ориентируя его так, чтобы конусная часть стопоров была направлена в сторону от вагона (сигнальные отверстия – в сторону корпуса сцепки);
- вращением винта клинового замка 6 произвести затяжку стопоров;
- установить зуб 5 на адаптер внешний 3 и зафиксировать его с помощью шкворня 4;
- повернуть шайбу на торце шкворня на угол 30.. .70° в любую сторону для предотвращения его выпадения.
Демонтаж адаптеров осуществляется в порядке обратном их установке.
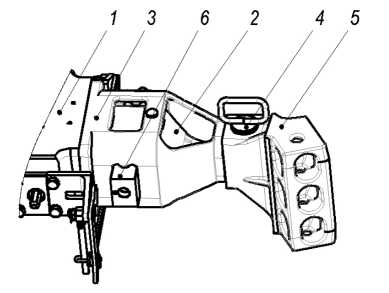
Рисунок 2.1.31 – Установка наружного адаптера: 1 – голова сцепки; 2 – центрирующий конус; 3 – адаптер наружный; 4 -шкворень; 5 – зуб; 6 – клиновой замок
Эксплуатационные ограничения
Ограничение скорости при прохождении участков пути:
- круговой кривой радиусом 100 м – до 5 км/ч;
- S-образной кривой радиусом 100 м с прямой вставкой не менее 20 м – до 5 км/ч;
- S-образной кривой радиусом 170 м – до 10 км/ч;
- минимальный радиус кривизны пути при прохождении в сцепленном состоянии не менее 100 м.
Относительная скорость соударения вагонов при их сцеплении должна быть не более 3 км/ч.
Допускаемые относительные смещения осей сцепок сцепляемых вагонов должны быть:
- по вертикали ±70 мм;
- по горизонтали ±80 мм;
- угловые смещения ±2°.
Рекомендуемые относительные смещения осей сцепок сцепляемых вагонов должны быть:
- по вертикали ±20 мм;
- по горизонтали ±50 мм;
- угловые смещения ±2°.
Угол отклонения оси сцепки должен быть в диапазоне:
- в горизонтальной плоскости: ± 16°;
- в вертикальной плоскости: ± 7°.
Подробно конструкцию, эксплуатацию и обслуживание – см Руководство по эксплуатации на систему пассивной безопасности ТМ130.00.00.000РЭ.
Подробности конструкции, эксплуатации и обслуживания системы пассивной безопасности – см. Руководство ТМ130.00.00.000РЭ.